makeSEA Propellers
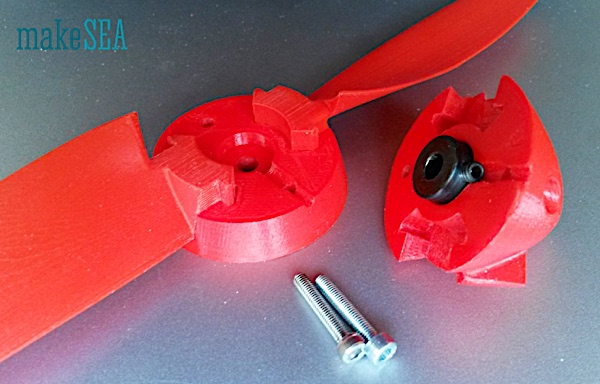
Propellers
(see also, Brushless Motor v2 re generator)
Idea / Motivation
Design a parametric propeller, useful as a fan or for an RC-plane.
Basically I wanted to know, if it is possible at all to create a 3d-printable propeller, which works with a satisfying efficiency. When successful it would be very useful, because pitch and diameter were freely adjustable, and I’m not restricted to the off-the-shelf propellers. The geometry of the propeller and the hub can be optimized for a specific the plane.
Implementation
The basic version of the propeller has 9 inch diameter and 4 inch pitch. The design allows to change both parameters, and also the number of blades from two to three (1 blade doesn’t make sense, and with 4 or more blades, the hub diameter needs to be increased as well in order to have enough space for the blade shafts).
Blades and hub are separated parts. The two or three blades fit tightly into the gaps of the two pieces from the hub. The hub encloses a shaft collar. The set screw of the collar is used as cam. The two parts for the hub are held together with two or three screws (depending on the number of blades).
There are various benefits of having separated parts:
- Printing orientation can be adjusted in order to optimize layers for the high centrifugal forces.
- The adjusted orientation for printing the blades makes it possible, that none of the support material touches the critical parts of the surface. A rough surface would disturb aerodynamics.
- Blades are printable in a single pass, and therefore they have all the same weight and distribution of mass, even if the filament diameter has small variations. This is relevant for having the assembled propeller well balanced.
- A propeller as one piece doesn’t fit into a common 3d-printer.
The image below illustrates the recommended printing orientation. As visible, it requires support material. The supported area at the front of the propeller is small and easy to sand. Anyway it is a good idea to also sand the surface of the blades. 400 grit with water gives good results.
As material I recommend using PETG (and not PLA). I fear the brittle PLA can break catastrophically at higher RPM, if there is a little shock. I didn’t do a test to figure out the limiting RPM, but the PETG-version did work well on a plane with a common brushless motor at 10’000 RPM.
Using the Propeller on an RC Plane
I’ve replaced a common 2 bladed propeller with the 3d-printed version. Both propellers had the same diameter and pitch. The plane has a weight of roughly 350 g and 700 g thrust (twice the own weight). Performance was almost unchanged - there was no noticeable difference during flight. On the ground, the 3d-bladed propeller draws a bit more current, but the flight duration was still similar.
Using the Propeller as a Fan
If the Propeller is used as a fan, I recommend to print also a guard. The most dangerous parts are the fast moving tips of the blades, because they can easily cut through human skin. For this reason the guard consists of a ring around the propeller. This ring has a proper airfoil as a cross-section, so it works as a duct (and maybe even improves the propeller efficiency).
The ring is too large for a common 3d-printed, so I divided it into 5 separate parts.
The next image shows how to orient the objects for 3d-printing.
Support material needs to be activated in order to print the overhanging structures.
The ring is held together by rails at the end of the spokes. Because of the angled orientation, the ring segments won’t slide out, when fully assembled. Fife small screws are needed to fix the spokes at the hub.
The holes in the hub are compatible with the 3d-printed brushless motor.
Additional Information:
- Guard: Ring for 9 inch propeller
- v1: First version is simpler to print, 9 x 4 inches, 2 blades hub
- v2: second version, better aerodynamics, 9x3 inch, 9x4 inch, 2blades hub, 3 blades hub - the same blades fit into the hub for 2 or 3 blades, and there are 2 types of blades with different pitch.
Related Video: RCPlane with 3-d printed motor and 3-d printed propeller
Download the Files for this Project
at the Mash Market HERE
Pictures and video don't convert like first-hand experience does.
Research shows that using augmented (AR), and virtual reality (VR), is more compelling and more likely to persuade your audience to buy, learn, and understand what you have to share. Use makeSEA to deliver content that connects with your audience like no other medium can.
Compel your audience with
Content Management and Cross-Platform Collaboration
for Augmented and Virtual Reality
The fastest way to organize and share your content as if you are together with your audience in real life and keep it fresh using next-generation virtual and augmented reality technology.
It's time to change the way you communicate, collaborate and compel your audience.
Time to change the way you capture and curate evolving ideas.
Use makeSEA content management platform + Catapult, our cross-platform client app for mixed reality and spatial collaboration to share your vision and inspire your audience with content that you are already producing.
10X-100X Time Savings • Recyclable Content & Scenes
Use makeSEA to reduce your AR and VR production time by an order of magnitude, or two.
Blend content from multiple sources tell a better story: 3D models, real-world scans, video, and you!
Keep things fresh and relevant and improve experiences over time as your content and XR technology mature.
Enabling augmented reality, mixed reality and spatial computing for everyday use.SM
Catapult your vision, in real-time together, for FREE.
It's as easy as a social media post:
-
Create an account, start a project and upload your content from most any content source1.
-
Launch Catapult, makeSEA's mixed reality client app on your VR or AR compatible device2.
-
Share and collaborate using your own spatial content, with others together in real-time, in the same physical space and remotely.
Click Here to Get Detailed Instructions, Download and Install
Try makeSEA now! Simply register here and start publishing.
makeSEA is also available as a privately branded (white-label), or custom integrated solution for enterprise. Please Contact Us for more information.
& Design
AR/Mixed Reality
Content Publishing
& Making
& Exhibits
& Branding
1:Catapult supports assets saved in GLB (preferred), FBX, OBJ, STL or MP4 (standard 720p, 1080p, or 3K 360˚ spherical surround format), or a makeScene package for live over-the-air collaboration with shared spatial content. See the how-to guide for hints and instructions on how to easily export or convert content from most 3D authoring tools and platforms. 2:makeSEA supports Oculus Quest 2, Magic Leap 1, and Microsoft Hololens 2, makeSEA for Enterprise supports additional client devices; contact us for more information.